Clean Fuel Impact: Elevating Microturbine
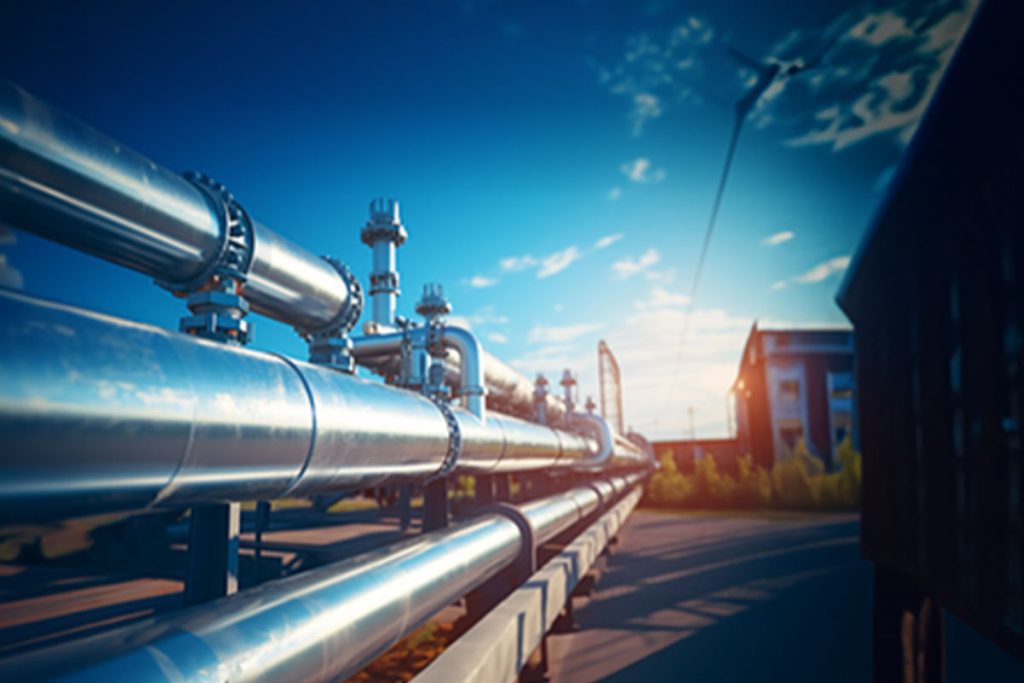
Clean Fuel Impact: Elevating Microturbine Performance, Maintenance, and Costs
Besides being one of the Big Three (air, fuel, ignition source) fundamentals for combustion, high quality, clean fuel has a significant positive impact on both the environmental and economic aspects of generator operation and system life. Power generation system owners and operators expect long system life and low operating cost. Let’s look at how fuel quality, and fuel conditioning maintenance, play major roles in meeting those expectations.
Rarely will a fuel be perfect as it occurs naturally. Chemicals harmful to finely machined microturbines may be present in both gaseous and liquid fuels. Some of these contaminants provide little, if any, combustion energy, making them undesireable in a microturbine engine. Fuel contaminants have the potential to cause the following issues:
- Fouled and clogged precision fuel flow control valve components. They can also plug fuel injectors and change the balance of fuel distributed within the engine, causing combustion instability and negatively impacting emissions.
- Fuel imbalances impact the internal engine temperature profile, which may lead to tip erosion of the turbine nozzle and turbine wheel, reducing microturbine performance. Furthermore, extensive tip damage may lead to sudden material loss, causing imbalances that may result in bearing failure.
- Liquid contaminants, including water, can contribute to combustion instability, leading to nuisance flameouts, in addition to negatively impacting engine emissions.
- Other liquid contaminants, such as compressor oil, or higher hydrocarbons, can cause injector damage, and if left untreated, may lead to significant damage to components like the turbine nozzle, recuperator and combustor liner.
Gaseous fuel composition varies depending on the source. Pipeline-quality gas is regarded as a suitably clean fuel (though particulate filtration is still required). Associated gas or gas derived from waste streams from industrial processes may contain various harmful constituents. Contaminants found in fuels include:
- Higher Hydrocarbons
- Compressor Oil
- Water and Water-soluble Compounds
- Hydrogen Sulfide
- Siloxanes
- Particulates (dirt, plant residue, bugs)
So, what is clean fuel? From the perspective of a Capstone microturbine, it is fuel that satisfies Capstone’s requirements for contaminant levels (i.e., a fuel that has been conditioned to the specific requirements of a microturbine).
Cleaning fuel at the end-user site is simple and requires: CONDITIONING. Simple – but not always easy. Conditioning systems can be as complex as the contaminants requiring removal. Whether simple or complex, all conditioning systems require regular attention and proper maintenance. For full system life, develop and follow a healthy maintenance regime for the fuel conditioning system, in addition to performing all necessary microturbine scheduled maintenance tasks according to the microturbines applicable scheduled maintenance guide.
Fuel Storage
Pipeline quality natural gas delivered to a power generation system does not generally present a storage challenge; however, applications requiring the use of LPG, unprocessed natural gas, or large processing facilities may require the use of large storage tanks and/or pressure vessels to ensure steady operation. In all cases, routine inspection and maintenance of the tanks and supporting equipment should be performed to ensure that the microturbine fuel remains available, clean and steady. Preventative inspections and service may prevent an unplanned outage caused by a failed pump or valve, and filtering the fuel for particulates/scale can ensure that downstream components remain in good condition.
For sites dependent on fuels storage/collection, proper maintenance may be the difference between optimal microturbine operation and the frustration of random, nuisance outages. Some fuel storage best practices may help prevent expensive and unplanned downtime include:
- Source fuel from suppliers with a reputation and proven track-record for reliability in delivering fuel to the agreed-to specifications.
- Routinely obtain fuel constituent reports from the supplier, when possible, or periodically sample and test the delivered fuels to ensure compliance. Notify the supplier of any descripancies to ensure a return to delivered specification.
- Follow best practices for personnel and equipment safety when receiving new fuel deliveries.
- Install and monitor data logs for fuel pressures, temperatures, and liquid levels to identify anomoloies that may indicage equioment issues.
- Use and maintain the approprote types of filters at each tank (e.g., particulate filters or coalescing filters).
- Check and maintain any condensate drain valves/lines to prevent condensate carryover to downstream equipment.
Service and Maintenance Benefits
Clean fuel, properly handled and maintained, is fundamental to long and efficient microturbine operation. The appropriate quality fuel, correctly conditioned, can result in optimal operation and reduced downtime, and deliver the full potential built into every Capstone microturbine.
Unfortunately, failure to properly condition the fuel for any power generation system can have a significant downside. The impacts of a dirty fuel may include the following:
- Increased episodes of unplanned maintenance.
- Additional unplanned maintenance costs in parts and labor, which also adds a level of uncertainty and lack of confidence in the equipment.
- Lower customer satisfaction levels due to increased down time and costs.
- Failure of critical microturbine components, such as valves and injectors, caused by the buildup of deposits, or general corrosion. Harm to these components may result in negative changes in microturbine performance, or the complete shutdown of a microturbine.
The benefits of clean fuel are many and include the following advantages:
- Clean, efficient operation meeting system specifications
- Increased end-user satisfaction
- Component life meeting or exceeding specifications.
- High microturbine uptime, maximizing the economic and environmental benefits of characteristics like CHP or the use of renewable fuels.
Proper fuel conditioning is vital to delivering a clean fuel to a Capstone microturbine in order to achieve optimal operation and longevity. It safeguards against contaminants that can harm crucial components, reducing maintenance costs, ensuring customer satisfaction, and minimizing environmental impact. Prioritizing the delivery of a clean fuel is a commitment to excellence and efficiency, allowing microturbines to fulfill their potential while being environmentally responsible.
Cr. https://www.capstonegreenenergy.com/turbine-talk/post/10073/clean-fuel-impact-elevating-microturbine-performance