Generator Painting: Process and Importance
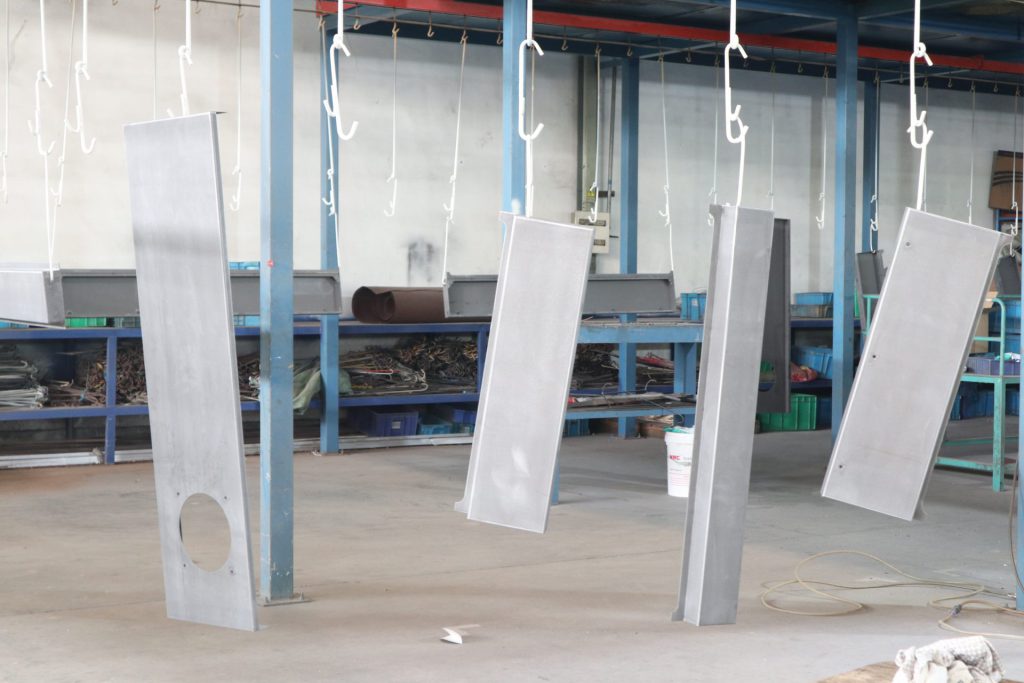
Why is Generator Painting Important?
Generators are essential equipment used to produce electricity for industrial plants, commercial buildings, or as backup power in emergencies. Due to exposure to different weather conditions and environments, painting a generator is a crucial process that helps protect the machine from rust, corrosion, moisture, dust, and sunlight, which can affect its performance and lifespan.
Proper painting not only enhances durability but also improves the appearance of the machine, making it look new and more appealing. Additionally, it can strengthen the brand image of manufacturers or generator installation service providers.
Steps for Painting a Generator
Painting a generator is not just about applying a coat of paint on the surface. It must follow a standardized process to ensure adhesion and long-lasting durability. The general steps for painting a generator include:
1. Surface Preparation
Before painting, the generator’s surface must be cleaned to remove dirt, rust, or chemicals that might prevent the paint from adhering properly. This step may include:
Sanding: To remove rust or deteriorated old paint.
Solvent Cleaning: To eliminate oil or grease residues.
Blowing Dust Off: Using high-pressure air to remove dust.
Chemical Treatment: In some cases, rust-removal chemicals may be used to prepare the surface for painting.
2. Primer Coating
After cleaning the surface, the next step is applying a primer coat, which helps the topcoat adhere better and prevents rust formation. Common types of primer include:
Epoxy Primer: Resistant to chemicals and moisture.
Zinc-rich Primer: Contains zinc to prevent rust.
Rust-inhibitive Primer: Provides long-term rust protection.
The choice of primer depends on the generator’s material and the environment in which it will be used.
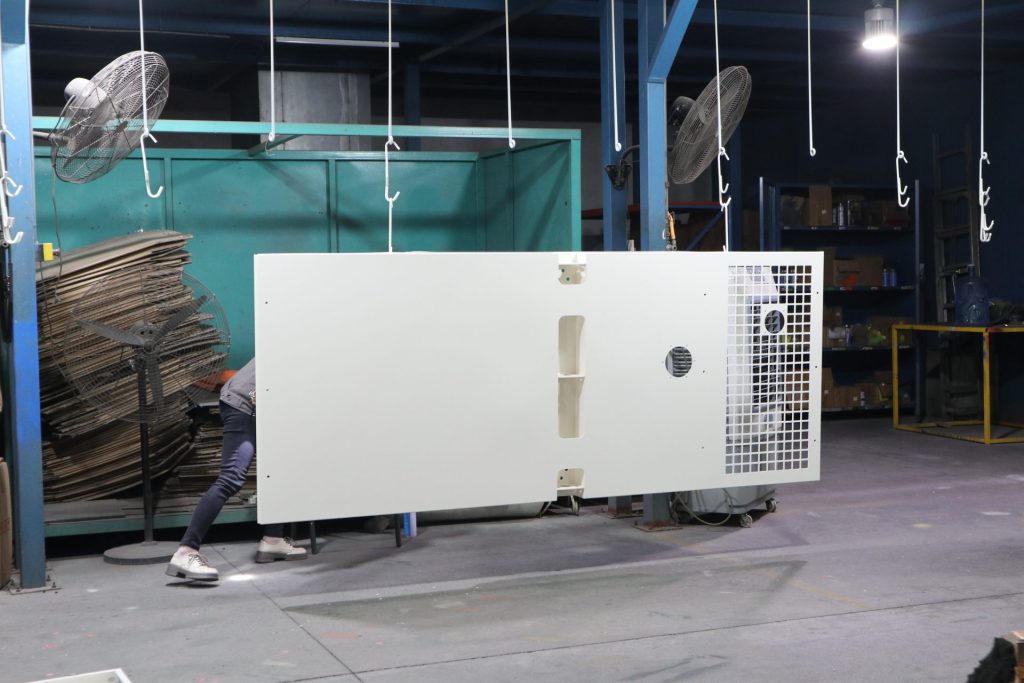
3. Top Coat Application
Once the primer dries, the topcoat is applied. This layer enhances aesthetics and protects the generator from environmental damage. Common types of paint used for generators include:
Polyurethane Paint: UV-resistant and chemical-resistant.
Acrylic Enamel Paint: Provides gloss and scratch resistance.
Heat-resistant Paint: Suitable for generators operating at high temperatures.
The chosen paint should be highly durable, as generators are exposed to various weather conditions such as rain, sun, and dust.
4. Protective Coating
The final step is applying a protective coating to increase the paint’s durability and prevent fading or peeling. Common protective coatings include:
Clear Coat: Enhances gloss and protects against scratches.
Anti-corrosion Coating: Shields against environmental corrosion.
UV-resistant Coating: Prevents paint fading due to sun exposure.
Benefits of Generator Painting
Proper generator painting according to industry standards provides several advantages:
Extends lifespan: Reduces rust and corrosion.
Enhances appearance: Keeps the generator looking new and professional.
Protects against environmental damage: Shields the surface from rain, sun, and dust.
Strengthens brand image: A well-painted generator reflects high standards and credibility.
Reduces maintenance costs: Durable paint reduces the need for frequent repainting.
Painting a generator is not just about aesthetics; it is a process that protects the machine from harsh environmental conditions and extends its service life. Choosing the right paint and techniques ensures long-lasting durability, reduces maintenance expenses, and enhances safety. If you are looking for a high-quality generator with a professional paint job that meets industry standards, make sure to choose an experienced manufacturer or service provider to ensure the best protection for your machine.
Cr. Multiphase Power